Lean
Manufacturing
LEAN MANUFACTURING
The search for profitability in organizations is driving the implementation of agile methodologies based on the principles of continuous improvement. Manufacturing companies are challenged with constantly verifying their processes to guarantee efficient operations, optimize costs, ensure product quality and achieve excellence in service.
With these efforts of continuous improvement and with the objective of increasing productivity, we provide support to our clients in the synchronization of their strategic objectives with the plant operations.
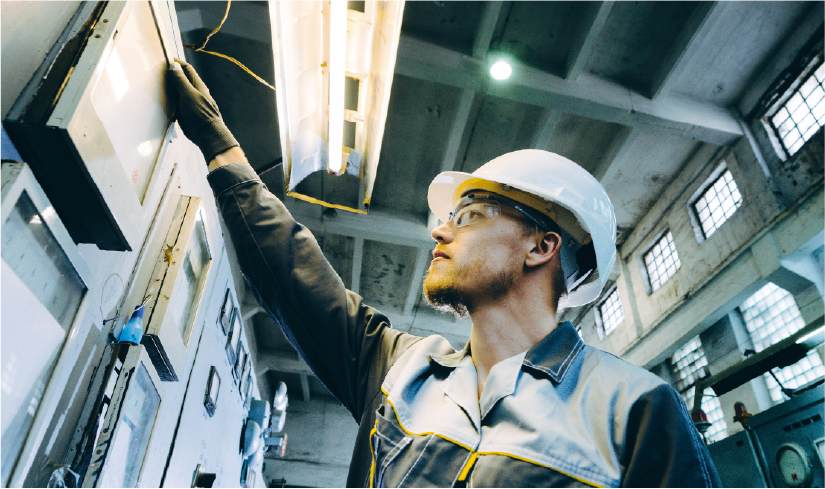
The Challenge
This manufacturing model requires not only the modification of production techniques to reduce waste and optimize resources but also it is necessary to the implementation of a culture of continuous improvement in production lines and jobs. Communication and teamwork are fundamental for the effectiveness of this method.
Some of the areas of opportunity that we have worked on together with our clients for the successful implementation of this model include the lack of planning aligned to the demand and purchase system, possible underutilization of machinery or overproduction, lack of definition of the adequate amount of human resource, poor floor control and maintenance planning and lack of control of quality assurance, among other factors.
01.
Production Planning
Solutions
- Calculation method for projection and determination of production standard times.
- Calculation and design of tools to generate the production plan.
- Decision tree for optimal sequence.
- Master plan to redistribute workloads.
- Mechanisms for effective coordination between the areas involved in the operation.
- Design of the typical day for the production planner.
Benefits
- Optimization of the use of machinery.
- Visibility of compliance in the level of service provided to clients.
- Production plan and program matching raw material inventories.
- Optimization of staff/personnel by adjusting it to demand seasonality. Master plan to redistribute workloads.
- Improvement in the coordination of operating areas and consequent preparation throughout the production chain.
- Improvement in active management of production scheduling.
02.
Floor Control
Solutions
- Active supervision model.
- Tour of the machines detailing the status of the condition of each.
- Design of floor control tools.
- Definition of indicators for production control such as OEE (Overall Equipment Efficiency), waste, compliance with the plan, etc.
Benefits
- Reduction in production costs.
- Increase in productivity and efficiency.
- Reduction of waste.
- Increase in compliance with the production schedule.
- Reduction in overtime.
- Better communication between areas.
03.
Maintenance
Solutions
- Preventive maintenance plan.
- Development of life sheets per piece of equipment.
- Definition and update of standard times for execution, control and follow-up.
- Setting parameters for replacement inventory levels.
Benefits
- Reduction of unscheduled machinery downtime.
- Greater availability of equipment and replacement parts.
- Increase in the distribution of time invested in preventive maintenance.
- Improvement in internal service level.
04.
Quality
Solutions
- Alert system that detects deviations of quality during production.
- Definition and update of standard times, frequency and quantity of analysis for its execution, control and follow-up.
Benefits
- Reduction of reprocesses.
- Reduction of rejections.
“Some of the results achieved include a 20% increase in the plant’s productivity, a 59% reduction in the percentage of repairs and a 51% improvement in quality through the efficient control of each of the production areas: cutting, sewing, inspection, finishing and embroidery.”
General Manager, Devanlay Lacoste, (Peru)
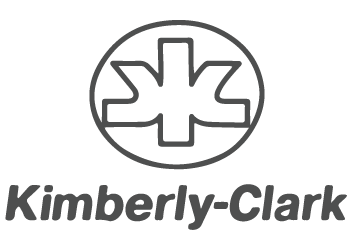
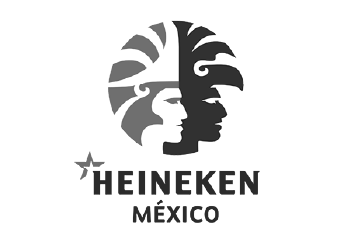
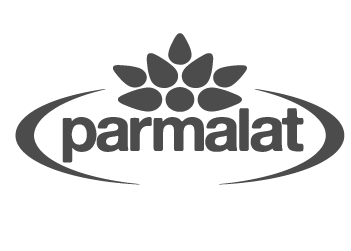

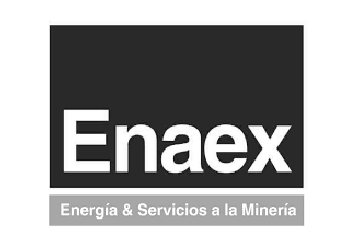
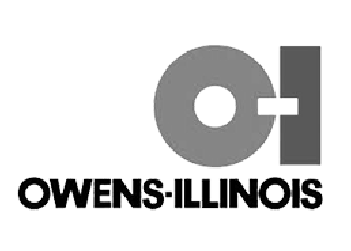
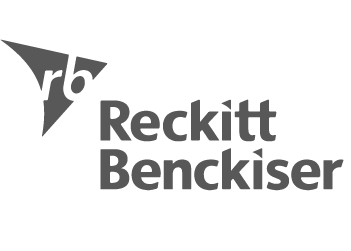