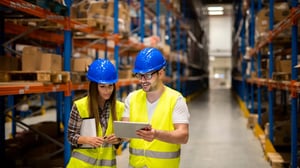
FROM TRADITIONAL OPERATION
BALLESTER HERMANOS
Since 1914, Ballester Hermanos has been synonymous with excellence in the distribution of food products in Puerto Rico. Representing more than 100 brands and serving more than 5,000 establishments, their commitment to quality and innovation has positioned them as market leaders.
In 2024, they decided to evolve their logistics operations with the MOB: Make Operations Better project, focused on their Dorado warehouse. The challenge was clear: improve productivity, consolidate processes and prepare their infrastructure for a more efficient, scalable and data-centric operation.
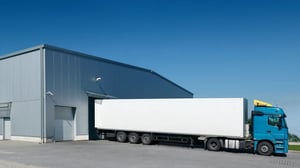
PROFESSIONALIZE PROCESSES AND SCALE THE LOGISTICS OPERATION
The steady growth of the Food Service division brought with it an urgent need: to structure warehouse processes, improve route planning and enhance operational control. The construction of a new distribution center was the perfect opportunity to redefine methodologies, tools and work standards in the key areas: receiving, warehousing, dispatch and distribution.
END-TO-END SOLUTIONS FOR A SMARTER SUPPLY CHAIN
- Digitized and system-integrated unloading plan.
- Automated time recording and productivity indicators.
- Audit and traceability error indicators.
- Loading Diagram digitalization and visualization for drivers.
- Management of loading time and returns.
- Productivity dashboards by employee and replenishment.
- Cycle Count model and over/shorts indicators.
- Document management and digital dispatch control.
- Optimized planning tools via Jotform.
- Checkpoints for overtime reduction and route traceability.
- Delivery indicators, route sequence and drop size per customer.
- Tools for new customer onboarding.
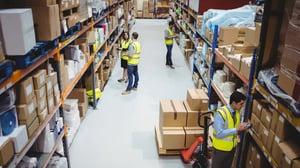
AN ORGANIZATIONAL TRANSFORMATION WITH DIGITAL TOOLS AND FOCUS ON RESULTS.
At London Consulting Group we not only redesign processes, but also enable collaborative and results-oriented work structures. Together with Ballester Hermanos' in-house team of continuous improvement, logistics and technology leaders, we executed a comprehensive plan that combined automation, operational analytics and change management, ensuring sustainable adoption across the entire logistics operation.
- Consolidation of information through dashboards and key indicators.
- Effective adoption of digital tools by operational staff.
- Governance model with management forums and action plans.
- Increased productivity and reduced logistics costs.
RESULTS
Productivity in replenishment and dispatching.
Lost sales due to dispatch errors
Returns due to warehouse errors
Driver overtime on route
Undelivered orders (returns)
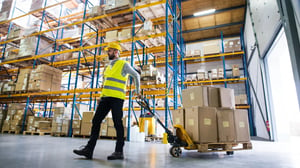
THE EXPERIENCE OF OUR CLIENTS WORKING WITH US
"I want to highlight the commitment and professional work of London Consulting Group's staff, who have worked under the highest expectation."
- Alejandro Ballester
President, Ballester Hermanos
WANT TO TRANSFORM YOUR LOGISTICS OPERATIONS?
Let's talk about how we can help you achieve measurable and sustainable results.