Manufacturers
LEAN ON US
Manufacturing companies are challenged with constantly verifying their processes to ensure operational efficiency, optimize costs, ensure product quality and achieve service excellence. In these continuous improvement efforts and with the objective of increasing productivity, we work with our clients in the synchronization of plant operations.
We identify and correct risk factors, such as not having planning aligned to the demand and purchases of raw material, the possible under-utilization of machinery or overproduction, lack of definition of adequate amount of human resources, inadequate floor control, lack of maintenance planning, lack of control in quality assurance, among other factors.
01.
Production Planning
Solutions
- Forecast calculation method and determination of standard production times.
- Calculation and design of tools to generate the production plan.
- Decision tree for optimal sequence.
- Master plan to redistribute workloads.
- Effective coordination mechanisms between the areas involved in the operation.
- Design of the typical day for the production planner.
Benefits
- Optimization of machine utilization.
- Visibility of the service level compliance given to customers.
- Production plan and schedule aligned to raw material inventories.
- Optimization of staff by adjusting to the seasonality of demand.
- Improved coordination of operational areas and their consequent preparation along the production chain.
- Improved active management of production scheduling.
02.
Floor Control
Solutions
- Active supervision model.
- Machine-by-machine walkthrough, detailing the state in which each machine is delivered.
- Design of floor control tools.
- Definition of indicators for production control such as TVC (Time, Speed and Quality), wastage, compliance with the plan, etc.
Benefits
- Reduction in production costs.
- Increase in productivity and efficiency.
- Reduction of waste.
- Increase in compliance with the production schedule.
- Reduction of overtime.
- Better communication between areas.
03.
Maintenance
Solutions
- Preventive maintenance plan.
- Development of life sheets by equipment.
- Definition and updating of standard times for execution, control and follow-up.
- Parameterization of spare parts inventory levels.
Benefits
- Reduction of unscheduled machine downtime.
- Increased availability of equipment and spare parts.
- Increased distribution of time spent on preventive maintenance.
- Improvement of the internal service level.
04.
Quality
Solutions
- Alert system that detects quality deviations during production.
- Definition and updating of standard times, frequency and quantity of analysis for execution, control and follow-up.
Benefits
- Reduction of reprocesses.
- Reduction of rejections.
“Some of the results achieved included a 20% increase in the plant’s productivity, a 59% reduction in the percentage of repairs and a 51% improvement in quality through the efficient control of each of the production areas such as cutting, sewing, inspection, finishing and embroidery.”
General Manager Devanlay Lacoste
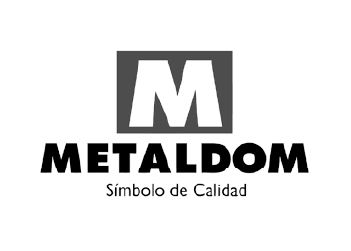
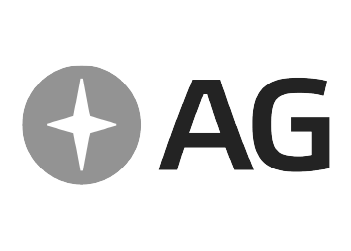
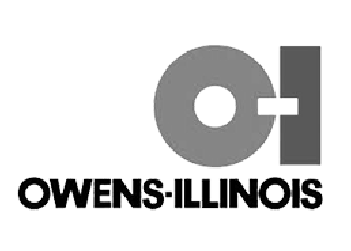
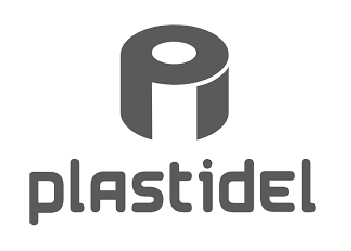
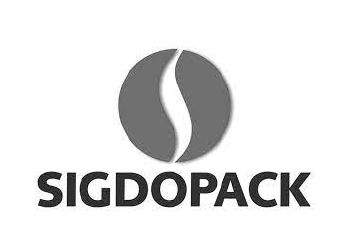
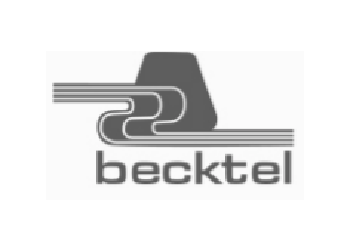
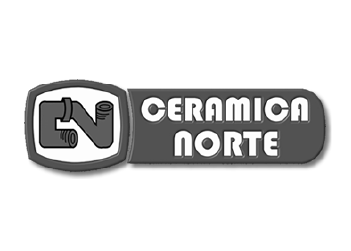
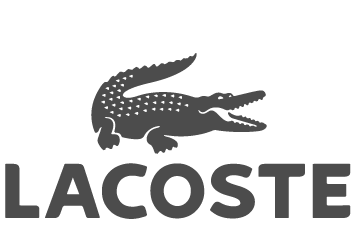
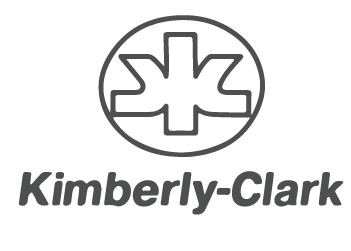
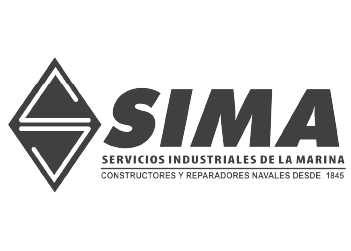
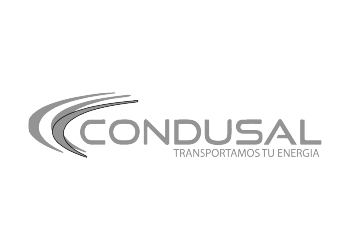
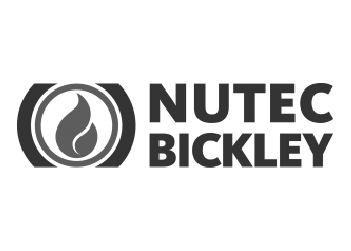